Yesterday, I tried to cast another font of 12-point Caslon Old Style (Lanston 12-337E). The computer and pneumatics worked flawlessly, but the type kept misbehaving in the type channel.
The caster seemed to be doing something known as a “second shot”, where a bit of molten metal squirts up and adheres to the foot of the type after the jet is cut off.
This metal causes the type to ride high in the type channel, not pack tightly to the adjacent type, or force the (spring-loaded) type channel to open up a bit and so allow the other properly-cast type to fall over or turn sideways. The type also jams as it transfers from the type channel to the galley. Sometimes the metal breaks off and is dragged into the type channel area where it prevents the type of lining up neatly.
There are actually two causes of extra metal at the foot of the type. The other cause is known as “bleeding feet” which occurs when the jet is cut off before the metal has solidified completely, and a bit of metal oozes out through the still-molten part of the foot of the type.
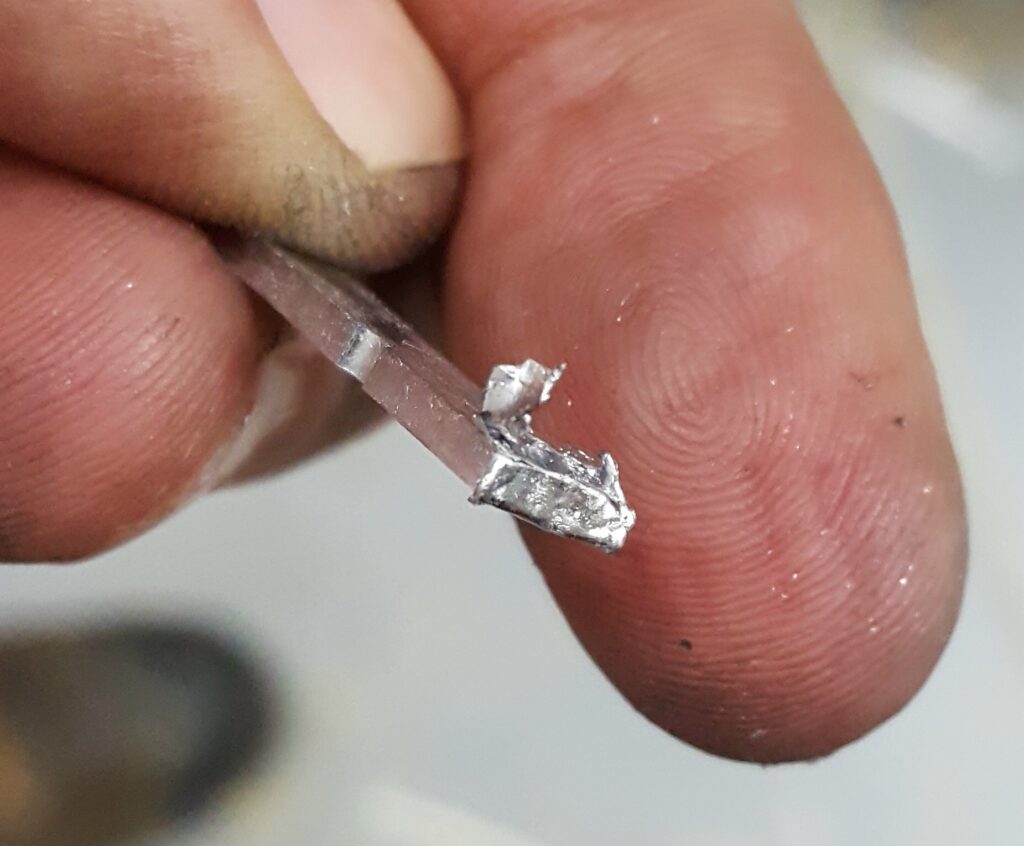
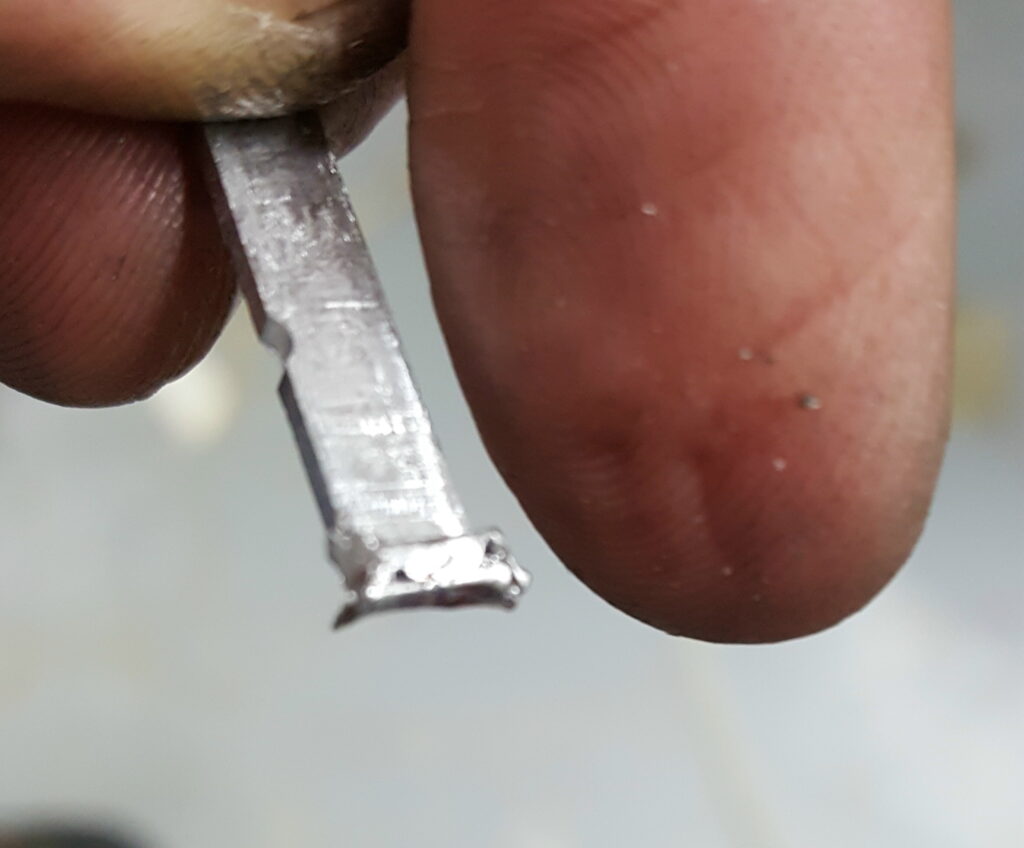
I have several reasons to think this is second shot and not bleeding feet:
- The caster is running borderline too cold as evidenced by the fact that in the same line as the bad feet I was also getting nozzle freezes. Bleeding feet occur when things are too hot.
- The extra metal almost peels off completely with only a tiny patch left adhering (though still enough to affect height-to-paper). I think bleeding feet would produce a solid well-adhered blob of metal.
- The metal looks like a squirt; it has the appearance you would expect from the “splat” of molten metal and looks like all the other metal decorating the floor and walls around the caster. Bleeding feet would tend to produce a compact, nearly round, blob of metal.
- The amount of metal exceeds what I would ever expect could ooze out of the foot of the type.
That being said, I’m at a loss to explain how this is happening. It has to be occurring after the type carrier and mould crossblock have moved completely to the right, exposing the foot of the type. By that time the pump has completely returned to its idle position. I only found one troubleshooting hint in the manuals relating to second shot, and it was a rather hand-wavy explanation of the source of the problem which did not really fit with how the mechanism moves. I’ll have to re-read that in detail to see if I can make sense of it. I’ll also review the timing diagrams I found in a (very old) manual to see the exact timing between the pump motion and the type carrier motion.
One strange thought I just had, related to the caster running borderline too cold, is that before the nozzle drops away from the mould, it (the nozzle) freezes just enough to seal it. After the nozzle drops away, heat conducted up from the nozzle base re-melts the metal, so any residual pressure in the area would cause a little squirt of metal. Again, I’d have to take a close look at timings to see if this is plausible (and still would need a theory on the source of the residual pressure).
Perhaps I could also take a slow-motion video of the pump operating to see if anything odd happens when a second shot occurs. The problem here would be identifying which pump cycles in the video had a second shot and which did not. Murphy’s law will of course dictate that if I try doing this the problem will go away!
The problem perhaps seemed to be worse when casting narrower type.
One problem analysis technique I sometimes use is to consider what has changed since last time (when the problem did not occur). Before this casting run I removed the pump body, cleaned the piston, chased oxides out from around the heating elements, drossed and cleaned the metal, and reinstalled the pump. I also topped up the metal, giving a very full pot. Serves me right for trying to run things sparkly clean!